中国轴承业"十一五“后的发展形势及重点
2019/5/19 18:38:38
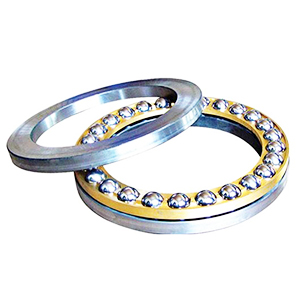
在总量上:到2010年,全行业轴承产量将达到80亿套,产品品种达15000种,销售额840亿元,工业增加值252亿元,全员劳动生产率55000元/人,单位工业增加值能耗比2005年降低20%左右,原材料综合利用率比2005年提高5个百分点。
在组织结构调整和优化上:培育2~3个年销售额50亿元以上和10个年销售额10亿元以上的大集团企业,20个产品有特色、年销售额3亿元以上的“小巨人”企业,6~8个规模化经营的轴承套圈毛坯、钢球、滚子、保持架和密封件等零部件专业化和工艺专业化生产基地。行业生产集中度CR30达到60%以上。
在产品结构调整和优化上:形成适应市场多层次需求,各个档次产品合理配置的产品结构,其中高端产品约占20%;中档产品约占50%;普通产品约占30%。主机配套率达到90%。部分企业部分产品达到具有国际竞争力的水平。
在技术结构调整和优化上:通过提高研发和创新能力,提高设计制造技术水平,使产品精度、性能、寿命和可靠性上一个大台阶。
总之,“十一五”全行业将从各方面做好准备,为跻身世界轴承强国行列奠定基础。
发展重点
重点发展为主机配套的中高档轿车用各类轴承、摩托车轴承、家用电器轴承、铁路车辆轴承包括准高速铁路客车和提速货车轴承、冶金矿山机械轴承、石油化工机械轴承、低噪声电机轴承、各类数控机床主轴用精密轴承、工程机械轴承、风力发电机组配套轴承等。
重点研究开发高新技术轴承。包括航空航天轴承、高速铁路客车轴承、新型轿车轴承、精密数控机床轴承、工业机器人精密薄壁轴承、办公机械专用轴承、冶金设备用精密长寿命轴承、环保型新型轴承、特种材料轴承和现行通用轴承结构改型等。
立足自主创新
充分发挥企业在技术创新中的主体作用
推动企业加强以技术中心为核心的技术创新体系的建设,力争“十一五”期间行业内国家级企业技术中心由5家增加到8家;创建省级企业技术中心20~30 家;企业博士后科研工作站由4家增加到7家;国家认可的中国实验室由5家增加到8家。制订和发布轴承企业技术创新体系和能力建设评价指标体系,开展评价活动,加强企业技术创新能力建设;引导企业建立健全专利、商标等自主知识产权的申报、管理、转让、保护等制度和运行机制,使企业的自主创新得到鼓励和保护;将自主创新指标列入企业主要负责人业绩的考核体系。
培养和造就富有创新精神的人才队伍
营造有利于企业创新人才脱颖而出的社会环境和体制机制;重点遴选和培养一批技术创新的领军人才;培育建设具有相当理论基础和创新精神的研发团队。
建立产学研战略联盟
发挥洛轴所、中机十院、河南科大在行业自主创新中的骨干和引领作用,通过政策扶持,强化其在研发、创新上为行业提供咨询服务和技术依托的功能;鼓励和推动企业与科研院所、高等学校实行产学研的有效结合,合理配置资源,有效整合优势,增强研发和创新能力。
实现基础资源共享
以技术中心协作网形式,实现大型、精密试验和检测设备、仪器以及基础信息等的有偿服务,资源共享。
基础理论研究整体跟进、局部突破
洛轴所、中机十院、河南科大和国家级企业技术中心、企业博士后科研工作站要瞄准国际先进水平,进行能引领未来发展的基础理论和前沿技术的研究,积极参与国际标准制订,力争在改变“两弱两少”上有所突破。
组织关键技术的研发
洛轴所、中机十院、河南科大牵头,有研发能力的大型企业参加,进行轴承关键技术和相关技术的研究开发。
调整产业组织结构
实施大集团、“小巨人”发展战略。通过公平竞争,做强做大一批,淘汰退出一批,不断提高行业生产集中度。一是推动哈、瓦、洛等大型企业深化改革、促进其由竞争走向竞合,形成战略联盟,打造我国民族轴承工业的“航空母舰”;二是推动哈、瓦、洛等大型国有企业发挥品牌优势,与民营企业优势互补,联手发展;三是推动成长性好的民营企业参与国有企业的改制和资产重组,盘活存量资产,做强做大;四是推动江苏、浙江两个省民营企业的合作联盟,培育产业集群;五是推动国内企业选择能真诚合作、达到双赢的合作对象,进入国外大轴承公司的全球采购体系。寄希望于一批熟悉国际国内市场、具有战略开拓能力和自强不息职业精神的优秀企业家和职业经理人,引领成长性好的优势企业做强做大,做优做久。
完善行政执法、行业自律、舆论监督、群众参与相结合的市场监管体系,健全产品质量监督机制。协会和各级工商管理部门、技术监督部门联手,组织企业开展打假维权活动;取得技术监督部门的支持,充分发挥国家轴承质量监督检验中心的作用,加大轴承质量国家监督抽查和行业督促检查的力度,定期发布轴承质量信息,引导市场,促使一批产品质量低劣的企业被市场淘汰出局。
转变增长方式
为了改变当前我国轴承行业粗放型的发展,中国轴承工业协会从“十五”开始即提出我国轴承工业要从规模增长型向质量效益型转变,“十一五”期间,全行业将加大转型力度,具体措施包括:
1.对产品市场前景好、国家政策鼓励的高精度、高技术含量和高附加值产品项目予以支持;要求固定资产投资项目,不但应有较好的经济效益,还要具有较好的社会效益和环境效益;项目产品的制造过程应做到资源、能源消耗小。
2.重点支持建立了现代企业制度,经营机制先进、企业效益好、竞争能力强、发展后劲足的大型企业集团和产品有特色的“小巨人”企业;支持具有较好的出口基础,产品专业化、零部件专业化和工艺工序专业化改造项目,提高行业专业化水平;重点支持科研院所、高等院校和大型企业集团和“小巨人”企业技术中心建设,进一步提高行业的技术创新和新产品开发能力;重点支持行业共性技术开发、技术攻关和高新技术产业化项目;支持中西部地区和东北老工业基地的发展。
3.继续组织行业共性技术的联合攻关。已取得阶段性成果的微小型深沟球轴承减振降噪攻关向广度和深度推进;已启动的滚子轴承减振降噪攻关和提高轴承寿命和可靠性攻关要打好攻坚战,达到攻关目标;开展提高滚针轴承精度、性能、寿命和可靠性攻关活动。
提升高效、高精度微小型、中型球轴承全自动生产线、中小批量中型球和圆锥滚子轴承柔性自动生产线及半自动、自动装配生产线在生产现场中的比例;研发和推广适用于轴承自动生产线在线检测用关键检测仪器;研发和推广批量生产Ⅰ级、Ⅱ级滚子成套加工工艺及装备;研发和改进轴承套圈冷辗、温辗工艺及装备;提高轴承热处理工艺及装备的整体水平;促进特钢行业提高轴承钢质量。
4.“十一五”期间在巩固已有5家中国轴承名牌产品的基础上,再创建6~8家中国名牌产品;争取再创建1~2家世界名牌产品。
5.加强以董事会为核心,出资人、董事会、监事会和经理层各负其责、协调运转、科学决策、有效制衡的公司治理结构,努力提升现代企业组织行为中的领导力。通过对市场需求和行业现状的系统分析,找准本企业的发展方向和目标,研究制订以“十一五”为起点的企业中长期发展战略,并进行有效的战略管理。摒弃陈旧的销售理念和低层次的竞争手段,大力加强以打造品牌优势、技术优势和服务优势为主要内容的战略营销管理。加强企业信息化建设,将信息技术运用于企业的核心业务流程;健全各生产要素管理的保证体系,以企业管理体系贯标认证为契机,促进企业各项管理的标准化,健全各生产要素现代化管理的保证体系。“十一五” 期间,企业要进一步夯实管理基础,优化业务流程,合理配置生产要素,提高企业素质,提高运营质量。通过整合物流、信息流、资金流和工艺流,加快由粗放式生产方式向精益、敏捷、集约的先进生产方式转变。
6.把人力资源能力建设和人才培养工程纳入企业发展战略,建立起吸纳人才、留住人才、激励人才、培养人才和用好人才的新型用人机制,搞好经营管理人才、专业技术人才和技能人才三支人才队伍的建设,尤其是高层次经营管理人才、高水平专业技术人才和高素质技能人才的培养。
面临形势
从国际上看,世界著名公司加快抢滩中国市场的步伐。到目前为止,国外跨国公司在中国境内已陆续建立了24家轴承成品生产企业,综合总投资约4亿~5亿美元,已初步形成8亿~9亿套轴承生产能力。现在的发展趋势是:一方面已建立的合资、独资企业不断扩大生产规模,加快实施人员和采购本土化,使得我国本土轴承企业原有的比较优势不复存在;另一方面,加紧深入到我国轴承行业的核心层、排头兵企业寻找合作伙伴,甚至控股、并购,尤以生产中小型球轴承为主向高端产品进发,占领技术制高点。有的还在我国建设研发中心、庞大的办事机构和完善的销售网络。这实际上把中国纳入跨国轴承产业链上的一环,把合资或独资企业作为跨国轴承公司的一个车间。对于我国轴承企业来说,这不是在同一起跑线上和同一层面上的竞争。我国轴承产业自主地位面临严重的挑战。
从国内看,近年来机械工业,尤其是轴承行业所服务的主机行业发展很快,并向高精度、高性能、高可靠性、高附加值发展。而轴承行业发展滞后,尚不能完全满足主机配套的需要。不仅在速度上,更重要的是自主创新能力差、开发能力不适应,产品结构不适应,制造水平不适应,技术含量不适应,以至这部分轴承只得依靠大量进口。比如,铁路轴承近几年来火车几次提速,目前客车时速160公里以上用的轴承全部靠进口;冶金矿山机械、工程机械,尤其是引进国外成套设备所需的维修轴承大部分进口;机床尤其是精密机床、数控机床的配套轴承也大部分进口;家电、空调机配套轴承80%进口。由于上述原因,导致近几年来轴承进出口顺差逐年减少,到 2003年首次出现轴承进口用汇额大于出口创汇额的少量逆差。
当前我国轴承工业发展正处于重要的战略机遇期。国务院颁发的《关于加快振兴装备制造业的若干意见》,明确提出振兴装备制造业的核心是自主创新和国产化。轴承是装备制造业的重要基础件,加快振兴装备制造业的战略决策为轴承工业的发展提供了契机。主机行业的快速发展为轴承行业提供了较大的市场空间,特别是对轴承需求量大的汽车、摩托车、农机、电机、电脑、家用电器、工程机械等主机行业的高速发展,国家重点工程建设如南水北调、西电东送、西气东输、北京奥运、上海世博会等项目的实施,对成套设备和工程装备的需求,均会相应带动和促进轴承工业的发展。
制约因素
一是自主创新能力低。全行业“两弱两少”,即基础理论研究弱,参与国际标准制订力度弱,少原创技术,少专利产品。设计和制造技术基本上是模仿,几十年一贯制。产品开发能力低,总体滞后于高端产品发展的需求,导致近些年来,进口轴承大幅度增长。2005年进口轴承用汇达13.6亿美元,进口增长速度高于出口增长速度
二是行业生产集中度低。在全世界轴承300多亿美元的销售额中,世界八大跨国公司占75%~80%。而我国瓦轴等7家年销售额10亿元以上的轴承企业,销售额仅占全行业的28.3%,前30家的生产集中度也仅为43.6%。
三是制造技术水平低。制造工艺和工艺装备技术发展缓慢,车加工装备落后,磨加工自动化水平低。对轴承寿命和可靠性等许多技术难题攻关未能取得突破。“十五”规划中的主要质量指标除少数先进企业外,尚有一定差距。